Junction to Heatsink Thermal Resistance for CAB011M12FM3
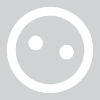
Hi,
We are using CAB011M12FM3 module in our Energy storage application.
We do see the Junction to Heatsink thermal resistance per MOSFET is 0.553°C/W in datasheet.
Please answer below questions
1) The Heatsink means here the Copper plate in the bottom side of the module or the external heatsink?
2) 0.553°C/W includes the thermal resistance if TIM material used between module and external heatsink?
3) How to calculate the temperature sensed by the NTC inside the module? Below method is correct?
T.j = 140°C - Junction temperature
Power loss per MOSFET = 50W
T.h = 140-(50*0.553) = 112.35°C
NTC Temperature = T.h
Please verify this method
Comments
-
Hi Prem,
Junction to heatsink is defined as from the junction through the package, through the TIM, and through 2mm of heatsink. For the module it was measured with grease with 6 W/mk thermal conductivity and follows our TIM guide. The heatsink was aluminum.
To correlate the junction temperature to the NTC temperature, there are 2 methods. The first is with physical verification on your end cold plate. You can run low voltage DC current (conduction only) through the module and utilize a fiber optic thermal sensor of a very small NTC/RTD and poke through the gel to gently contact the die. With the die temperature measurement you can then correlate to the NTC reading.
The other way is to use a thermal simulation to correlate the temperature. We have thermal models that can be shared under NDA to perform this simulation.
The reason there is no straight forward answer is because the correlation of the NTC temperature to the die temperature is highly dependent on the end system's thermal performance. If you have very good cooling, there will be a large delta between NTC temperature and die temperature. If the end cooling solution is poor, the NTC temperature and die temperature will follow more closely.
Thanks,
Dan
0 -
Hi Dan,
Thanks for explaining the situation.
We would require the thermal models for running the thermal simulation. There should be a NDA already in place. Could you please let us know how to proceed further to get the model.
0 -
Hi Prem,
Yes we will contact you with next steps.
Thanks,
Dan
0