CAB016M12FM3 for drone application, humidity altitude, top hole, press-out fixturing
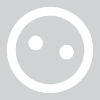
Hello,
I wanted to ask if there is any technical information regarding the operating environment for the CAB016M12FM3? Of special interest would be the maximum altitude and the maximum humidity (eventhough it will be placed in a sealed housing).
Additionaly I wanted to ask why there is a hole on the top-side of the housing (big one next to the pins)?
Would it be possible to receive the CAD files for the Press-out fixturing? I have already found the Press-in fixturing in another post.
Thanks a lot in advance and best regards
Matthias Neuner
Comments
-
Hello Matthias,
High humidity and condensation can ingress into the module and cause increased leakage and/or failures. Condensation can be especially troublesome if it is able to collect and drip into the module housing after significant amounts of time below the dew point. It may be possible to control these environmental issues at the system level with a climate control system that monitors humidity/temperatures and adjusts added heaters/fans as needed. More information is available in our Environmental Considerations for Power Electronics Systems Application Note, available in our document library and linked below.
The WolfPACK housing has a minimum CTI of 200, so it is considered a Material Group IIIa. The minimum clearance and creepage distances are listed on the datasheet. With this information and your system requirements, IEC 60664-1 may be utilized to determine clearance and creepage requirements based on voltage and altitude. Specifically, see Table A.1 and A.2 for clearance and Table F.4 for creepage. The pollution degree is determined by your system.
As an additional note, forced-air cooling effectiveness is reduced as altitude increases, so additional thermal requirements may need to be considered depending on what altitudes the system may encounter.
The top-side hole on the WolfPACK module housing is a fill hole for potting material to be dispensed into the module to provide voltage isolation and inside the module during our manufacturing process.
The press-out fixturing is attached to this post and detailed in our WolfPACK Mounting Application Note, available on the document section of WolfPACK module product pages and linked below. Press-out fixturing is much simpler than the press-in fixturing. A top flat plate either mounts/clamps to the press-fit equipment or can even rest loosely on top of the module pins if placed properly. The press-in profile is then performed, which exerts a force on the pins protruding from the top of the PCB surface until they are pushed out of the through-holes. A base with cavity provides support around the module perimeter and allows the module to drop out once the pins release from the PCB. It is recommended that the top plate be metal as the point contacts from pins may puncture plastics.
Please ensure you review Section 3 of our WolfPACK Mounting Application Note regarding the possibility of repeated press-in of a WolfPACK module and a PCB; a WolfPACK module should only be pressed-in once.
https://assets.wolfspeed.com/uploads/2021/11/cpwr_an41_fm3_mounting_application_note.pdf
Thanks,
Brett
0 -
Hello Brett,
thanks a lot for the clarifaction and the files! This really helped a lot and I only have one question left: Does the press-out process damage the PCB itself (I could imagine yes after the 10th time, but let's say after the first time) or better said is the PCB still usable after the press-out?
Thanks a lot for the good support and all the best
Matthias
0 -
Additionally: Could you may send me the DXF files for the stencil (for TIM)? I have seen that they are available upon request. Or can I buy the finished stencil somewhere?
Thanks again!
0 -
Hello Matthias,
From the FM3 mounting application note, PCBs that are designed according to the guidelines may have a WolfPACK™ series module pressed in up to three times – that is, the module can be replaced up to two times. After the third module is removed from the PCB, it is recommended that the PCB be replaced. Furthermore, once a module has been pressed into a PCB and removed, its press-fit functionality may be hindered and it is recommended to solder the module pins to the PCB.
Please note that the boards hole quality may need to be verified. If plating and copper quality in the holes are lower than requirements, the holes could potentially sustain damage during press-out and not be suitable for a repeated press-in of a different module.
Please find a DXF for the present FM3 stencil design in the ZIP attachment. You may find more details about the TIM application process and stencil guidance in the CPWR-AN42 FM3 TIM Application Note document linked below.
Thanks,
Brett
0 -
Hello Brett,
thanks a lot for all the clarifications!
I have just one question left: I am trying to place a driver PCB located on top of a DC-Link PCB (where the modules will be pressed in) and connect them with low profile headers (Gate and Source). Now the question arised what the minimum recommended distance between the tip of the press fit pins and the bottom layer (let's say with a conducting plane) of the driver PCB should be (currently in the preliminary design it is ~2.80 mm as can be seen in the picture below) in air (including altidude and humidity). Are there any recommendations regarding isolating material between the PCB's?
Thanks a lot again and all the best
Matthias
0 -
Hello Matthias,
If pressed-in using a 12.45mm gap as mentioned in the mounting application note in my first response, the center of the press-fit zones on the module pins should land in the middle of a 1.6mm PCB. Please see Figure 21/22 to observe where the PCB is expected to rest on the pins.
The center of this zone is well above the PCB in your image, indicating the module 3D CAD was placed incorrectly in z-axis of the PCB, the press-in process being used is significantly deeper than intended, or a very thin PCB is being utilized (which is not recommended for this style of power module). Any of these will result in the pins protruding from the top surface of the PCB far more significantly more than intended.
Please see this forum post for an example of press-in fixturing for a generic FM3 power module, noting the distance between the 12.45mm edges of the top and the base surface is 1.6mm. If you place one of the FM3 STEP modules against the flat surface on the top fixture and fill in the 1.6mm gap with a transparent extruded rectangle to represent a PCB, you can see where the press-in zone should contact the PCB.
Thanks,
Brett
0 -
Hi, I hope that this answered your question. I will close this discussion for now but if you have a follow up question, please "Start a New Discussion" and we would be glad to support you further.
0