Thermal hot spot test of XM3 module and connection reliability between module and driver board
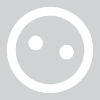
Hi Sir,
Can you provide test guide how to get the hot spot inside the XM3 module by NTC, since threre is temperature gap between NTC and hottest Die.
another question is how to design the connection reliability between driver board and driver board, since vibration test is required and what is vibration level for our XM3 module and CGD12HBXMP driver board, thanks.
Comments
-
Thank you for your post, it has been approved and we will respond as soon as possible.
0 -
Hello Tangwei,
As the NTC is closely coupled with the case as opposed to the die, it is extremely difficult to gauge what the hotspot/hottest die is within the power module using the NTC.
We recommend determining the hotspot and hottest die through two methods. Firstly, Finite Element Analysis (FEA) using an accurate geometric and material model of the module’s layout can be useful to determine the criteria. Multiphysics software such as COMSOL employ FEA to perform thermal analyses to illustrate how heat is transferred in a system.
Lastly, the lid from the module can be physically removed along with the encapsulant material, so that the die are visually exposed. When the module is under testing, a thermal camera can be used to capture the infrared footprint of the heat, indicating hotspots. For this method, it must be noted that inside the modules must be coated with a high emissivity (0.9-0.95) non-metallic paint so that the highly reflective surface of the die does not interfere with the heat detection by the thermal camera.
0 -
Hi ShamarChristian,
thanks for your great support and detailed reply for thermal evaluation method.
Besides, our customer found driver pin of XM3 module would wear out during vibration test (driver board connect with module), so can you give some mechanical design advice to strengthen the connection reliability, thanks
0 -
The module itself is quite stiff and solidly mounted to the cold plate. It is designed to operate in a vibration environment, but the system design needs to account for vibrations effect on the interfaces. The interface between the gate board and module is a connector with a spring member that presses against the pin. This connector is not fixed and is susceptible to motion between the module and gate card. The gate PCB is a flat plate supported by stand offs / system structure, it will respond to system level vibration similar to a drum head, the amplitude and frequency of motion depending on how it is supported, how thick it is, mounted components, materials used etc. This up and down motion will vary in amplitudes and frequencies in different areas. If the gate connection is in an area of fairly large motion it will oscillate up and down the pin, rubbing between the pin and spring member, creating tribological wear at the interface. This wear can lead to an intermittent contact or complete open.
This sort of issue is the domain of system design and requires an understanding of the systems’ vibration environment as well as the detailed design. The vibration response of the PCB can be modeled in a finite elements analysis or using simple analytical methods available in the literature. Experimentally a system level vibration test could be run to look for this sort of interaction as it is not always easy to predict where issues will occur. In general, stiffening the PCB and/or moving support structures can shift the nodes and modes of vibration to alleviate this problem. Mounting the connector/PCB so that the connector does not have the opportunity to oscillate is a good approach. This could be by ensuring that the PCB/connector header is in compression on the module housing in all vibration regimes.
0 -
Thanks a lot for such detailed reply!
0 -
Hi, I hope that this answered your question. I will close this discussion for now but if you have a follow up question, please "Start a New Discussion" and we would be glad to support you further.
0