Assistance Required with CRD300DA12E-XM3 GUI, Firmware, and Code Migration
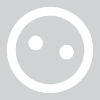
Hello,
I have recently purchased the CRD300DA12E-XM3 evaluation board and downloaded the GUI and firmware from the Wolfspeed website. I followed the steps provided in the User Manual to interface the board with the recommended Korlan USB2CAN adapter.
However, I am facing the following issues:
- When using the GUI, even after enabling all logics, changing any variable does not result in output pulses on the controller's EPWM pins. (with the pre-flased code)
- The CAN communication between the GUI and the board frequently breaks after some time.
- I also attempted to migrate the firmware downloaded from the Wolfspeed website to the F28379D controller. However, the provided files do not appear to include a complete project.
Could you please provide the complete project files for the F28379D controller, specifically for open-loop operation of this inverter?
Additionally, I would appreciate any suggestions or troubleshooting steps to resolve issues 1 and 2 (no output pulses and unstable CAN communication).
Thank you for your support.
Comments
-
Thank you for your post, it has been approved and we will respond as soon as possible.
0 -
Hello deepak,
I addressed your questions individually below:
- Even with all the outputs enabled, the EPWMs will not begin switching if the modulation factor is set to zero. Please ensure that the modulation factor value is non-zero. Furthermore, are you getting a response from the controller? For instance, when you change a value in the inputs fields, are you observing the same value in the response fields? It's possible that the issue is with the CAN communication, and the board is not receiving any of the changes.
- The is likely a signal integrity issue with the CAN connection to the board. To reduce the risk of disconnecting, I recommend the following. First, use high-quality cables for all the connections to the board. Cables with strong shielding are preferred. Second, wrap several turns of the cabling through a large common-mode (CM) choke. This will help with the signal integrity. The best location for a single choke would be as close as possible to the inverter; however, adding a choke close to the inverter and close to the CAN adapter would be even better. Third, reduce the length of the cable to as short as possible that ensures the operator is a safe distance away. If the cabling is unnecessarily long, it may be causing this CAN disconnecting issue.
- The firmware on the website has been downloaded and implemented by many users. It contains all the files required to re-flash the firmware. Perhaps the correct supporting libraries have not been properly configured? Please follow the instructions in Section 6 of the user guide to properly configure the Code Composer Studio environment.
Thanks,
Chris N.
0 -
Hi, I hope that this answered your question. I will close this discussion for now but if you have a follow up question, please "Start a New Discussion" and we would be glad to support you further.
0