Questing about CRD300DA12E-XM3 with CGD1700HB2M-UNA gate driver power supply
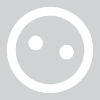
Hello Experts,
We were looking at the CGD1700HB2M-UNA schematic and we had a few more question on the UCC21710 gate driver power supply design.
There is an isolated DC/DC converter (R12P21503D) which is +15v/-3v (93mA/185mA) which is used to generate the positive and negative voltage rails to turn On/Off the mosfet module.
But we see that the output of this DC/DC converter are again given to voltage regulators, the LT3015EDD#TRPBF of the negative rail and the LT3082EDD#PBF for the positive rail, and then they go to the gate driver(UCC21710), Why is this done so? Using a higher current rated regulator(the LT3015 is rated for 1.5Amps) has no meaning if the input is current limited to a few mA? and, In case of the negative regulator , the input -3v (185mA), what is the purpose of RB7? As per the BOM RB7 is assembled and it would directly bypass the negative regulator?
Texas instruments provides a tool to see what are the gate driver current requirements for UCC21710. Putting in the values that were in the CGD1700HB2M-UNA circuit we get a maximum source current of current of 4.29A and a maximum sink current of 4.7A. How are you achieving such high levels of current? I don't think the isolated DC/DC converter can achieve these currents even momentarily..
Could you kindly clarify on the above.
Thanks,
AK
Comments
-
Hello AK,
RB7 is utilized to bypass the negative regulator. The schematic you are referencing shows both the regulator & the bypass resistor populated simultaneously; this is not an intended use case. Either the regulator can be used or the bypass resistor must be installed, but never both at the same time. The stock gate driver comes with the bypass resistor populated. The negative regulator allows customers to study the effect of a range of -VGS on switching performance if the need arises. It also allows for a stable, regulated -4 V rail if a MGJ2D121505SC is populated in the isolated DCDC position. Please see the schematic below showing the 'do not populate' (DNP) components.
The current supplied by the gate driver IC to turn on the power module occurs in an extremely small time window, which is typically less than 100 ns. The remaining time during the period, the gate driver IC is not supplying current. The large gate current pulse does not come from the DC supply; the high di/dt pulse is composed of high frequency content that must be sourced from a low impedance source such as capacitors located near the driver IC. This is why we include multiple 10 µF bypass ceramic capacitors located as physically close to the power pins of the UCC21710 driver IC as possible. Nearly all of the gate pulse current (up to 10 A peak) is supplied from these capacitors.
As for the selection of the regulators, they're included to provide flexibility of the gate rails for the user to conduct tests under various VGS conditions. If you attempt to use a MGJ2D122005SC and drop the +20 V rail down to a regulated +15 V to ensure the driver provides a constant, stable +15 V, you'll need a higher rated regulator to dissipate the heat from this large drop. This is an evaluation tool designed to make your life easier in a lab setting as opposed to a highly cost-optimized reference design. There are absolutely tradeoffs that could be made to optimize the driver's design for other design factors.
Best Regards,
Austin C.
0 -
Hi Austin,
Thanks for the schematic, that clears things up.
We are planning on using the UCC21710 as the main gate driver for our custom inverter hardware and we would like to use the CGD1700HB2M-UNA design as a good starting point. One more point that we wanted some clarification on , the current design of the CGD1700HB2M-UNA is optimized for using the SiC power module (XM3 module). Would the design also be valid/compatible for an IGBT module?
We plan to use a similar gate driver design in our 20Kw inverter , but it should be compatible to both SiC and IGBT power modules.
Could you shed some light on what major changes if any, do we need to make and consider if we are using a IGBT module. The IGBT has a relatively higher gate charge compared to an SIC power module..
Thanks,
AK
0 -
Hi AK,
Assuming the voltage rail recommendations for the SiC MOSFET and the IGBT modules are the same, then yes, this driver design would be valid for both technologies. You should double-check your driver's power requirement based on the the IGBT module's gate charge and your application's maximum switching frequency. The short circuit protection of the IGBT module may also be tuned differently than the SiC MOSFET-based module. For the SiC MOSFET, priority should be placed on turning off as quickly as possible to minimize the short circuit energy, but for the IGBT, the voltage overshoot is also important to consider, so a 2-level turn-off or soft shutdown implementation may be beneficial.
Best Regards,
Austin C.
0 -
Hi, I hope that this answered your question. I will close this discussion for now but if you have a follow up question, please "Start a New Discussion" and we would be glad to support you further.
0